Toparts analysis with you Hydraulic cylinder Seals application
Understanding the role of lubrication is the first key to successful sealing in dynamic systems. A fully lubricated system will experience some leakage, usually in the form of a fluid film, but friction will decrease, leading to a corresponding decrease in seal wear. Not surprisingly, the opposite is true: In a sparsely lubricated system, the fluid film decreases, but friction—and thus, wear—increase.
Moreover, sealing tends to improve as fluid pressures increase. Because system pressure on the seal surface compresses the seal axially, the seal is forced more tightly into the gland, improving conformability of the seal with the metal surfaces around it. If the seal is correctly designed, as system pressure increases, sealing force and effectiveness also increase.
A seal’s ability to resist extrusion is a third key factor. Seals in dynamic systems must resist shear forces resulting from the differential between the pressurized and unpressurized sides of the seal. Shear forces tend to push the seal into the gap between adjacent metal surfaces (known as the clearance gap), and the seal material and profile must be sufficiently strong and stiff to resist being damaged or destroyed.
Toparts is a professional design and production of hydraulic cylinder seal kits suppliers mainly for r Komatsu, Caterpillar, Hitachi, Kobelco, Sumitomo, Daewoo, Doosan, Volvo, Hyundai and other large mining models with hydraulic seal kit
Rod Sealing
Leak-free performance and high service life cannot be ensured by a single sealing element in heavy-duty applications. Because the cylinder’s piston rod is directly exposed to the environment, it’s paramount that the seals keep the fluid in the system. External leakage is easily noticed. Not surprisingly, then, it has become a common criticism of hydraulic power transmission.
The solution is redundant systems that involve specially developed seals arranged in a series, often referred to as in tandem. Each sealing element in such systems has a specific function, and their interaction is critical to a high-functioning system.
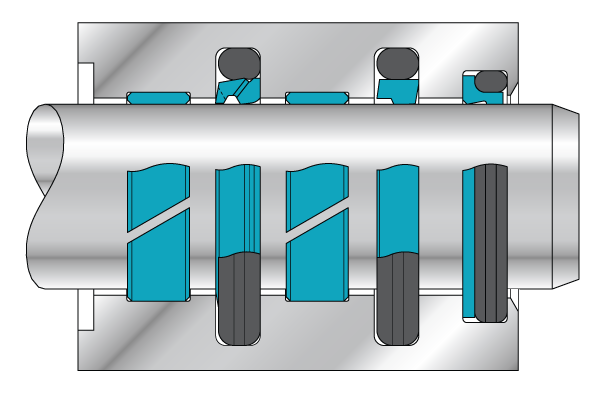
This illustration shows a variety of piston rod seals to make an effective sealing system. At left and center are tandem wear rings, at far right is a rubber-energized double-acting scraper seal, and the other two are single-acting O-Ring-energized rod seals.
Two main configurations are recommended for tandem sealing systems. The first is a vented unidirectional polytetrafluoroethylene (PTFE) slipper seal with either a unidirectional PTFE or polyurethane slipper seal as the secondary seal. This configuration has the advantage of limiting micro fluid-film formation under the seal and ensuring that when the rod is retracted, the sealing face supports hydrodynamic back pumping of the fluid film. This results in leak-free sealing with low friction for decreased wear. Additionally, the secondary seal materials described above provide superior sliding ability with maximum wear resistance.
The second configuration is a buffer seal, which has an integrated backup ring and a polyurethane U-cup as the secondary seal. This arrangement is usually more cost-effective than the first option and may suffice for systems requiring high abrasion resistance or where pressure will continually fluctuate between high and low pressure. A modified version of the buffer seal also can be used to provide lubrication for the U-cup so it does not run dry.
Rod scrapers—Contamination of the hydraulic fluid is the most common cause of damage to seals, rings, and other components. O-ring energized scrapers and double-lipped polyurethane scrapers are recommended for dynamic sealing systems, with the choice depending on the type of contaminants expected and the friction and stick-slip requirements of the overall system.
O-ring energized scrapers are composed of PTFE or another thermoplastic material and are installed with an elastic O-ring in one groove. The O-ring maintains the pressure of the scraper lips against the sliding surface, which compensates for deflections in the piston rod and allows effective scraping of contaminants—even firmly adhered dirt.
Double-lipped polyurethane scrapers are superior to conventional elastomeric scrapers, with a scraper lip designed to effectively remove dirt while leaving the oil film required for correct operation. The sealing lip faces inward to assume a sealing function under low pressure, and the static seal is achieved by a tight radial fit between the scraper body and the groove.
Piston Sealing
Choosing a piston seal should be based on its wear and gap extrusion resistance, compatibility with the hydraulic fluid, operating temperatures, sliding ability, and ease of installation. The mating surface is also a key consideration—specified limits should be observed since they can greatly affect the piston seal’s service life.
Three types of bi-directional slipper seals are recommended for dynamic piston systems: either a PTFE or polyurethane seal with an optimized cap profile based on the material or a seal with a PTFE cap that contains an integrated elastomer element. The choice depends on the media to be sealed and the desired friction performance of the system.
- PTFE slipper seals are ideal for applications requiring low friction and no stick-slip or where larger allowable clearance gaps are present.
- PTFE slipper seals with an integrated elastomer element are ideal for situations where fluid separation or tight leakage control are required.
- Polyurethane slipper seals offer high abrasion resistance and are a good fit for situations where blow-by could be a concern.
-
PTFE slipper seal shown in a vented unidirectional configuration.
When redundancy against leakage is required, unidirectional slipper seals or polyurethane U-cups can be added on one or both sides (depending on pressure direction and/or fluctuation) of the bidirectional seal to further prevent leakage and ensure media separation.
Wear Rings
Wear rings absorb side-load forces occurring on the piston or piston rod of a cylinder and eliminate metal-to-metal contact between the sliding parts of the cylinder. Non-metallic wear rings offer significant benefits over traditional metal rings. Non-metallic wear rings have a longer service life, higher load-bearing capacity, lower friction, and good scraping effects. They also damp mechanical vibrations to reduce noise and are cost-effective.
In terms of material, PTFE-based wear rings are recommended for low- to medium-duty applications with limited radial forces. The low friction of PTFE rings provides smooth operation at low speeds without stick-slip motion. These rings should be selected for high wear resistance and good damping capability.
Rings composed of glass-filled nylon are recommended for applications with medium- to heavy-duty radial forces. Look for rings offering high compressive strength at high temperatures and easy installation on pistons and glands.
Fabric-reinforced composite wear rings are the best choice for heavy-duty applications with high radial forces. These rings should distribute high radial forces evenly and exhibit good sliding and dry-running properties, good scraping effect, and high wear resistance.
High-Pressure Cylinders
Corner-reinforced seals are an excellent choice for high-pressure applications (up to 15,000 psi) because they are highly resistant to extrusion. These seals contain an integrated ring made of poly ether keytone (PEEK) or polyacetal and can accept 50% to 100% higher extrusion gaps compared to those without corner reinforcement.
Corner-reinforced seals perform well in high-pressure applications.
PTFE and polyurethane seals are available with corner reinforcements for both rod and piston configurations. Some are designed for unidirectional use while others provide bidirectional sealing. In unidirectional seals, look for versions that are designed to stabilize the seal against back-pressure by preventing the seal from tipping forward in the groove.
Mating Surface Finish and Coatings
Many design engineers are aware of the importance of mating surface finish on seal functionality. The mating surface’s finish can greatly impact:
Friction and heat—The rougher the surface of the hardware, the greater the amount of friction and heat generated.
Wear—Rougher surfaces lead to more wear, as do hard surfaces.
Sealing ability—The rougher the surface, the less effective the sealing ability.
Long-term cost cost—Field failures and repairs are expensive, so long-wearing, high-performing seals ultimately save money.
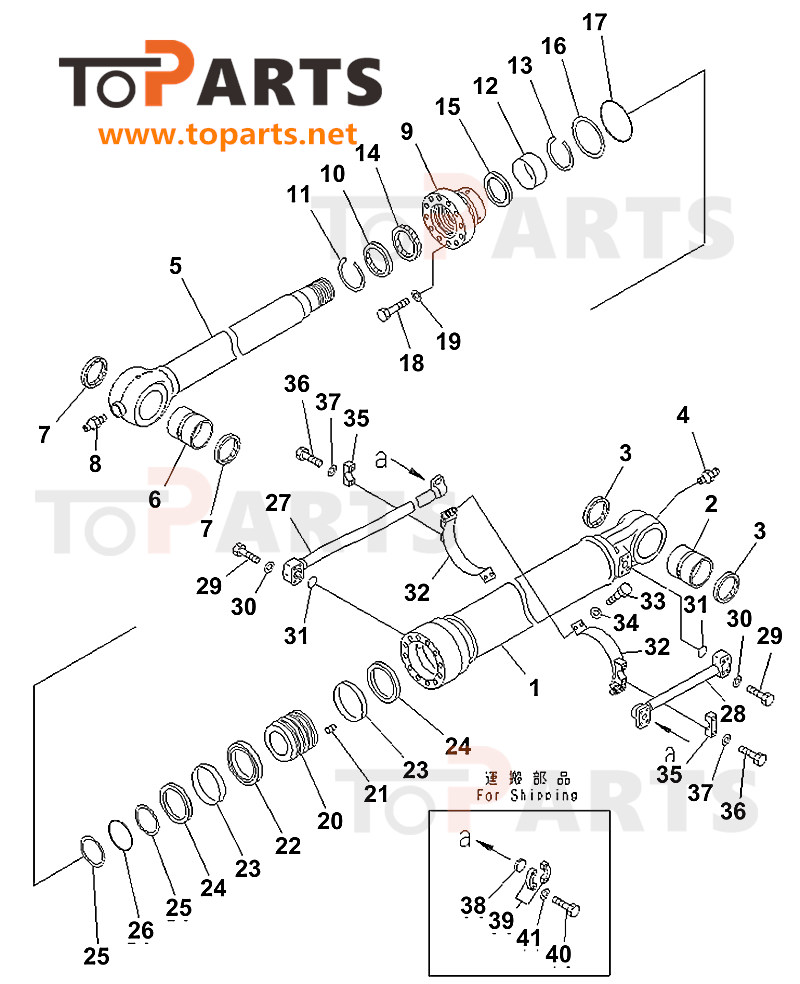
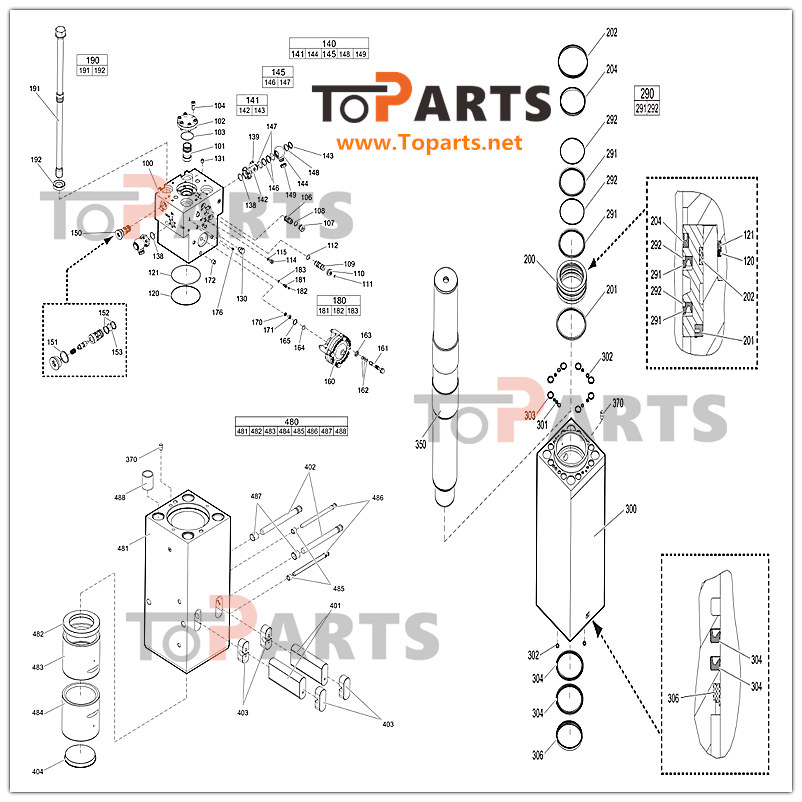
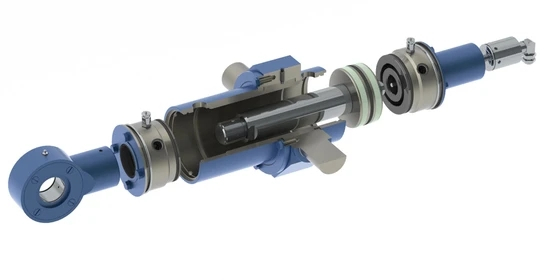
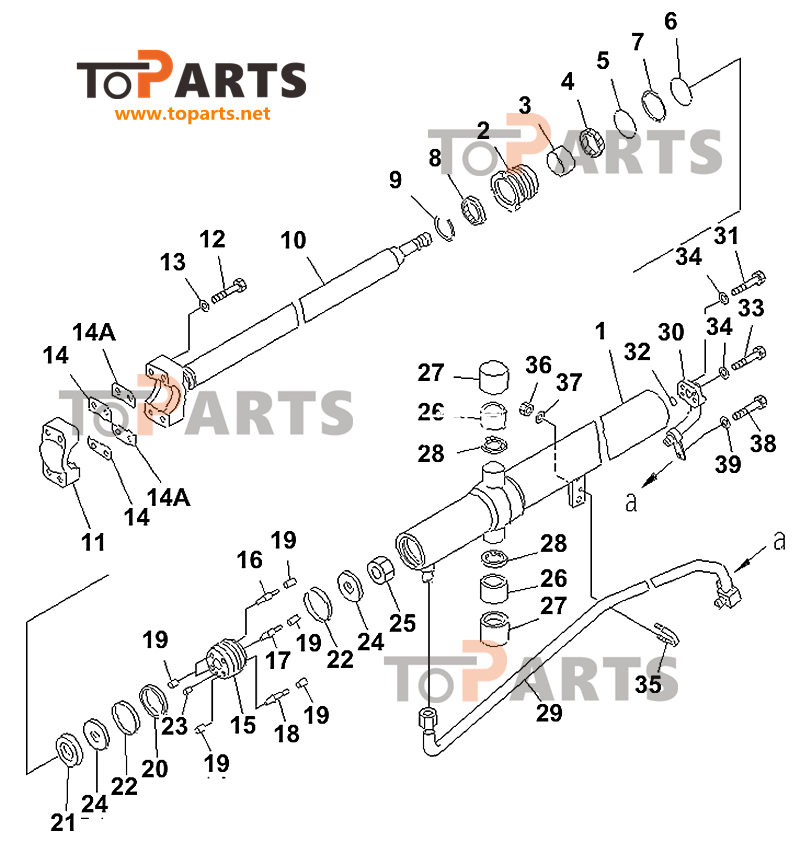